Enhanced Scalability and Durability of BPs for Heavy-Duty Vehicle Applications
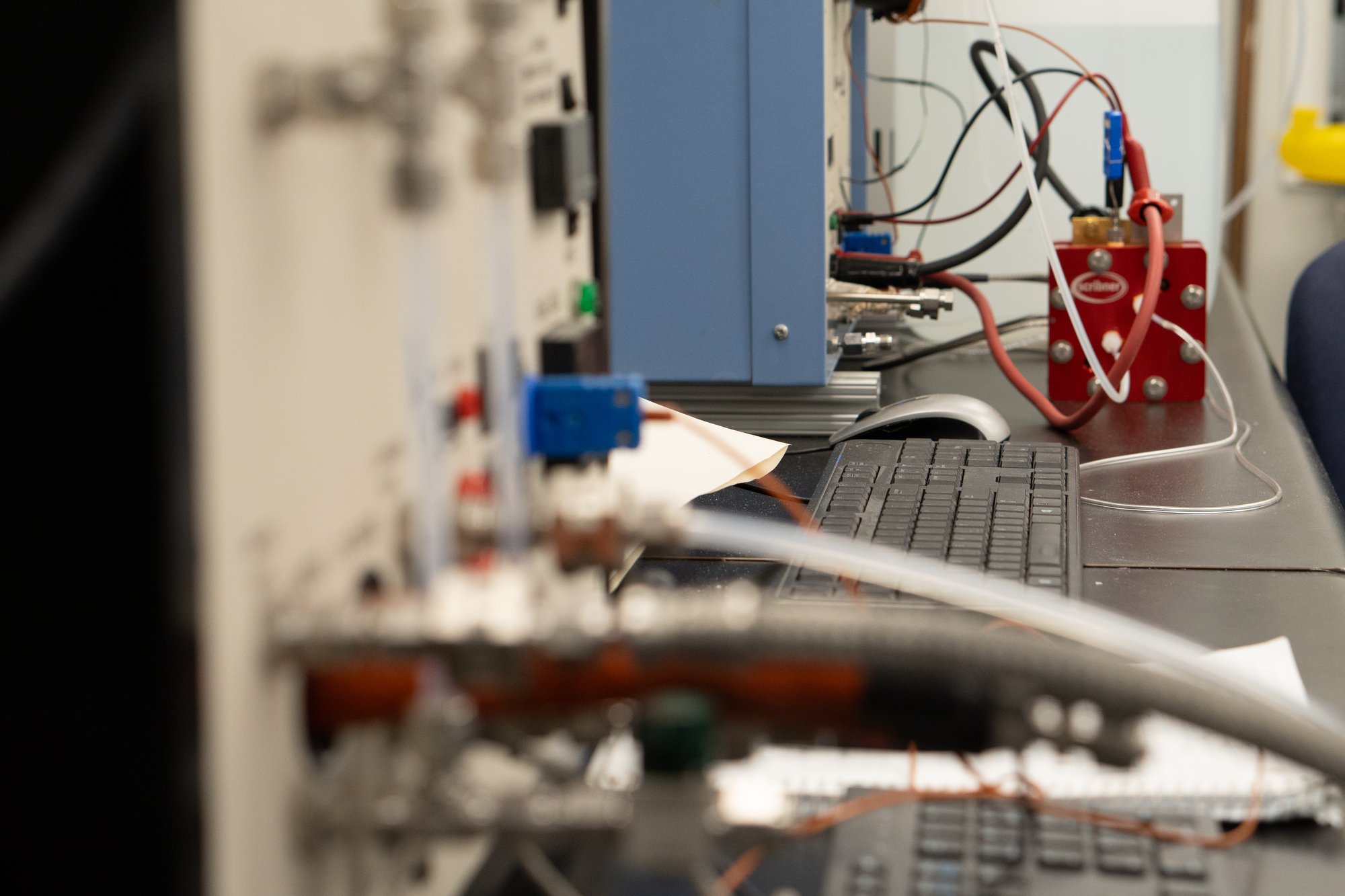
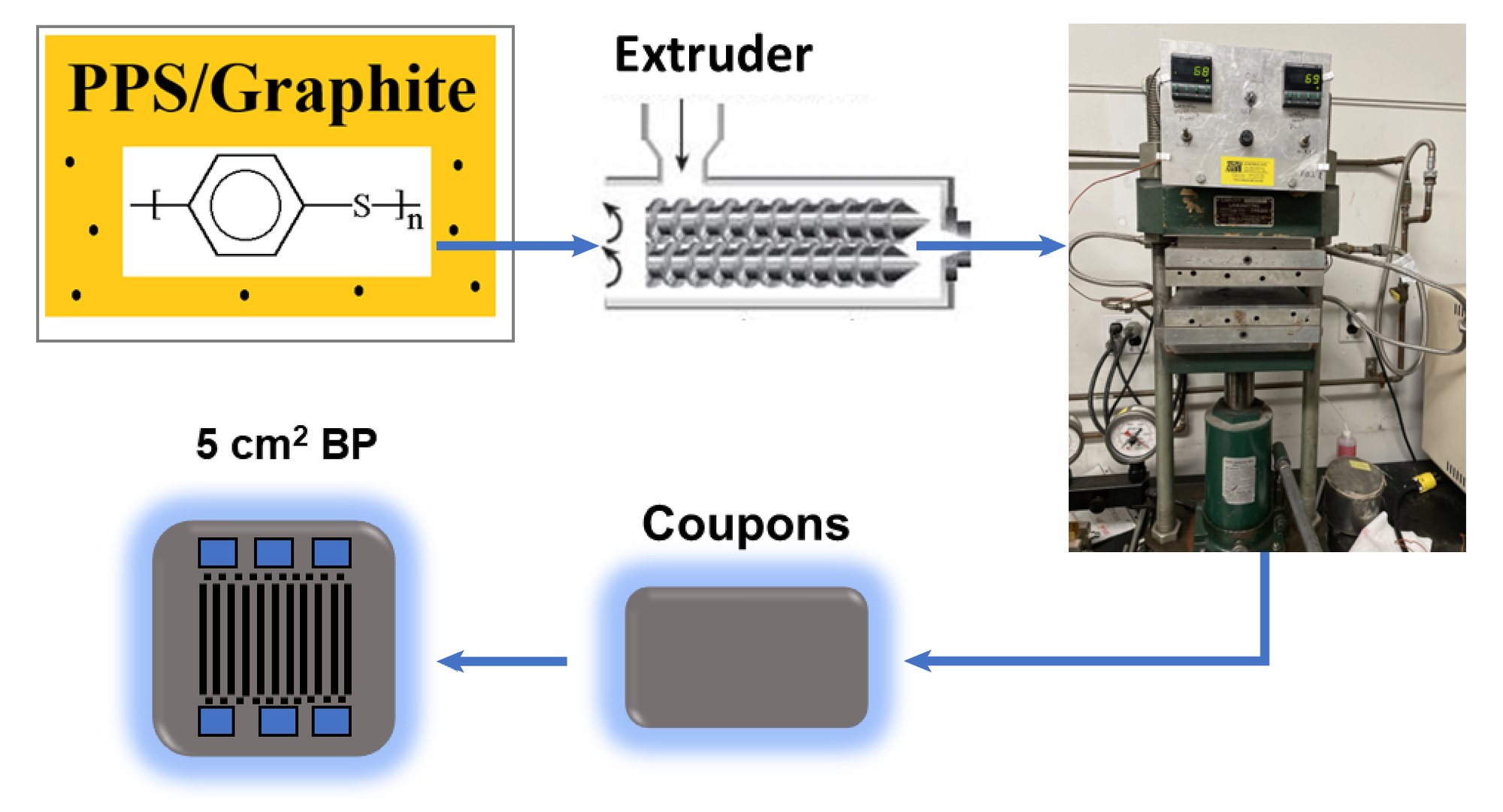
Requirements for Bipolar Plates
A bipolar plate serves as a separator with gas flow channels on each side, a current collector, as well as heat dissipator, that provides mechanical strength to the stack. BPs are projected to be the second most expensive PEM fuel cell stack component in scaled-up systems and can represent 20 to 40% of the stack cost. Furthermore, BPs can contribute up to 80% of the total stack weight. Metal, carbon or their composites are the main materials for BPs. Metal BPs are generally made of stainless steels, titanium or copper, which need to be coated with conductive materials such as graphene, nickel, chromium or nitride containing films, to alleviate conductivity loss due to passivation of the metal surface, as well as corrosion.
Carbon Composite Bipolar Plates
Carbon-based plates offer low material cost, negligible corrosion, and advantages in formability, but currently have lower strength and must be thicker than metal plates, resulting in lower stack power density. Giner focuses very specifically on the composite materials used to make bipolar plates. The idea is to generate ultra-thin, light-weight bipolar plates using a graphite-loaded thermoplastic using a high-performance polymer like polyphenylene sulfide (PPS) that can withstand the PEM fuel cell operating conditions while still meeting performance targets. Special additives are used to aid in the increase of the amount of carbon used to improve blending. Carbon nanotubes are added to improve electric conductivity and mechanical strength. The continuous graphite structure helps achieve high thermal and electric conductivity.
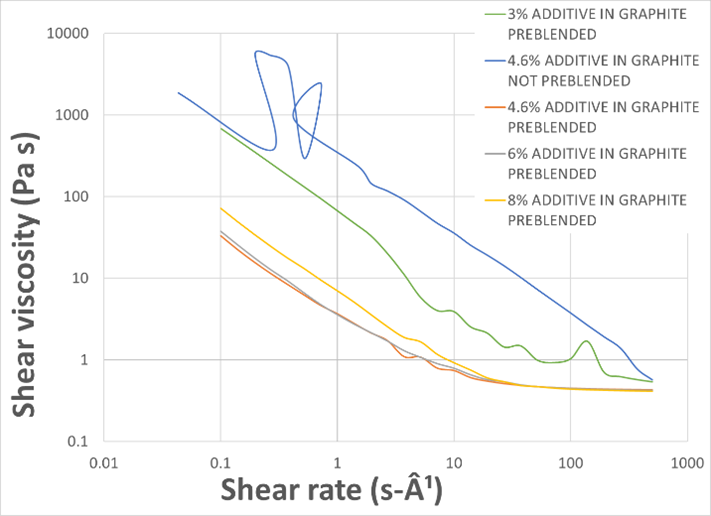
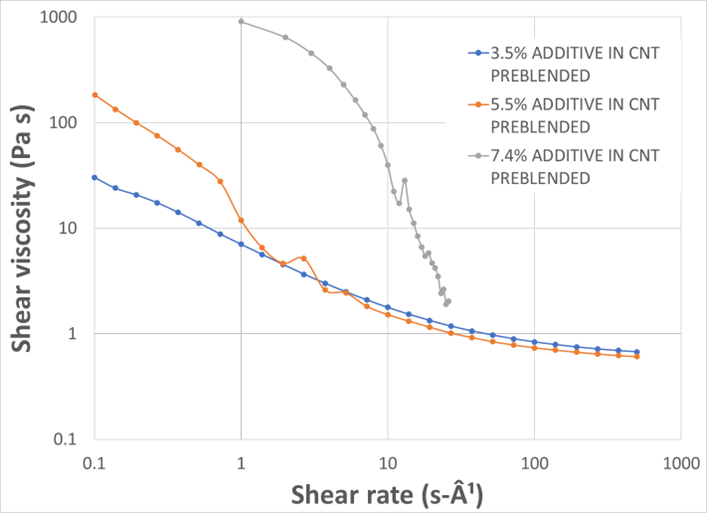